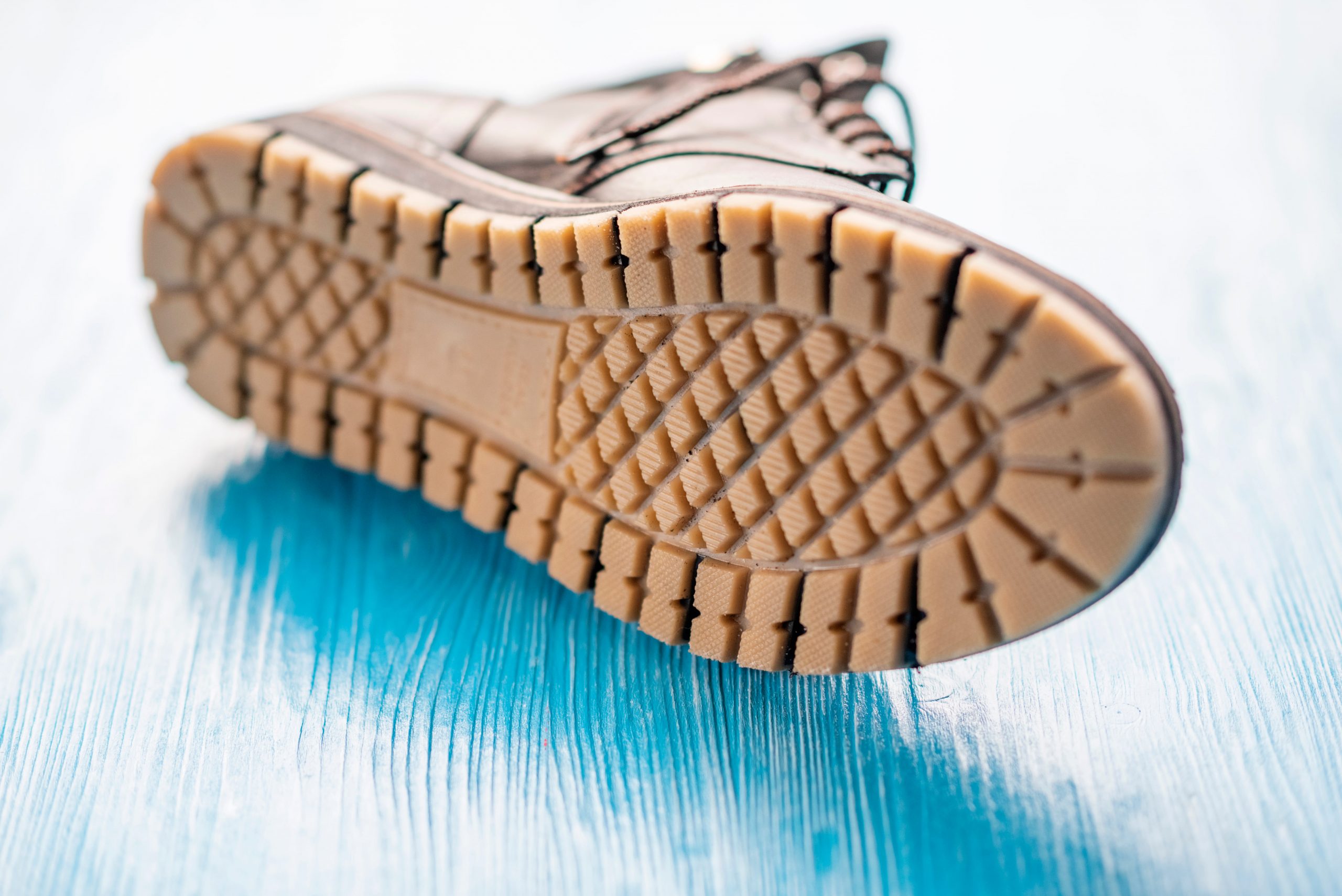
Poliuretano para calçados: aplicações e tecnologias do PU no mercado calçadista.
Tempo de leitura - 5 minutos
Quando falamos em poliuretano para calçados, pensamos em uma alternativa que oferece flexibilidade, durabilidade e conforto. Além disso, o poliuretano oferece uma ampla gama de possibilidades de design, permitindo a criação de calçados estilosos e modernos.
Graças à sua versatilidade, o uso do poliuretano para calçados vem se popularizando na indústria. De acordo com dados da Associação Brasileira das Indústrias de Calçados (Abicalçados), houve crescimento de 15% na produção de calçados com solados de poliuretano nos últimos dois anos.
A Associação das Empresas de Componentes para Couro, Calçados e Artefatos (Assintecal) também realizou, em parceria com o Sebrae, um mapeamento de materiais mais utilizados em 2022, que aponta que:
- Os cabedais de laminados de poliuretano respondem por mais de 40% do total produzido;
- No forro do calçado, o componente mais utilizado pelos fabricantes também é o laminado de poliuretano (60,65%).
Agora que você já sabe sobre o potencial de crescimento deste mercado, continue lendo para descobrir as principais vantagens e aplicações do poliuretano para a indústria calçadista.
Aplicações do poliuretano para calçados
As tecnologias de poliuretano para calçados são inúmeras, podendo ser utilizadas na fabricação de diversos componentes, como:
- Solados
- Entressolas
- Palmilhas
- Lingueta
- Saltos
Dadas as suas propriedades de resistência e flexibilidade, o PU é amplamente utilizado em diferentes modelos, como por exemplo:
- Calçados esportivos;
- Sapatos masculinos de boa qualidade;
- Sapatos femininos (principalmente os de sola tipo plataforma);
- Entressolas de tênis sofisticados;
- Calçados de segurança (bi-densidade);
- Palmilhas especiais;
- Entre outros.
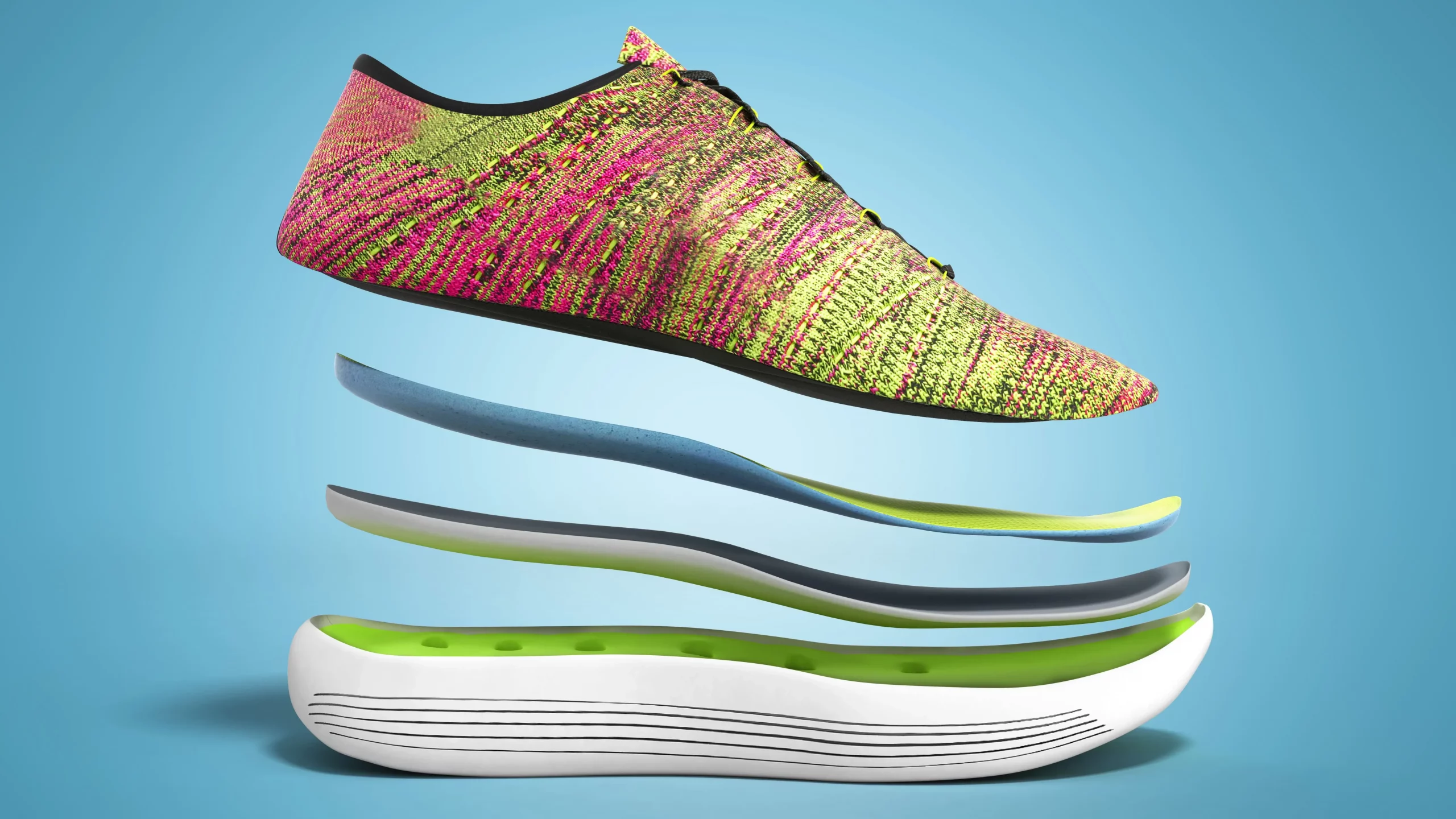
Vantagens do PU para o mercado calçadista
As tecnologias do poliuretano vêm sendo utilizadas há anos na fabricação de solados e outros componentes devido a fatores, como por exemplo:
- Alta resistência à abrasão, flexão e rasgo;
- Elasticidade;
- Propriedades antiderrapantes;
- Flexibilidade mesmo em temperaturas baixas;
- Propriedades termofixas (não amolecem com o calor);
- Isolamento térmico;
- Baixo peso do calçado (devido à baixa densidade do solado);
- Durabilidade e conforto;
- Processo simples que garante alta produtividade;
- Perfeição de cópia (imitação de cortiça madeira, couro, etc.);
- Permite injeção direta em cabedais, com extrema facilidade para variação de densidades;
- Processo em baixas temperaturas e pressões;
- Menor custo e alta vida útil dos moldes;
- Facilidade de tingir;
- Versatilidade na adequação à moda;
- Produção de componentes flexíveis e/ou rígidos.
Diferenças entre tecnologias de poliuretano para calçados
Poliól poliéster
Os sistemas poliéster são os mais utilizados em solados, pois possuem maior resistência à abrasão, rasgo, tração, graxas e solventes.
Por outro lado, têm menor resistência à hidrólise e micro-organismos, e as matérias-primas sólidas ou semissólidas requerem processamento à quente.
Todavia, a excelente resistência à abrasão, os torna os sistemas preferidos para solados de alta durabilidade.
Quando a resistência a óleos e solventes é uma necessidade para aplicações com especificações rigorosas, como, por exemplo, a dos sapatos de segurança, os sistemas a base de poliéster são a escolha preferida.
Como os poliuretanos à base de poliéster são mais sensíveis à hidrólise, com o envelhecimento, as propriedades físicas podem ser influenciadas negativamente, e aditivos podem ser usados como estabilizadores, porém podem ter impacto no custo.
Poliól poliéter
Os sistemas poliéter possuem menor viscosidade e, por conseguinte, melhor processabilidade, maior resistência à hidrólise, e maior flexibilidade a frio, devido à menor temperatura de transição vítrea (Tg) do poliéter.
Estas características são desejáveis para a manutenção da maciez e a fim de evitar rachaduras em entressolas, com a durabilidade requerida para aplicações esportivas de alto desempenho, que é medida pela perda de espessura (deformação permanente após 30.000 e 50.000 ciclos de compressão a 75%) sob condições normais de uso por um determinado período de tempo.
Com os sistemas poliéter, diversos componentes de calçados podem ser fabricados, possuindo peles de várias estruturas, como imitações de couro, costuras, cortiça, madeira; etc.
A dureza da superfície pode variar desde a da madeira, nos sistemas empregados em tamancos, até flexível como nas entressolas, calços e palmilhas ortopédicas.
Atualmente, a previsão é de que 943,7 milhões de pares de calçados sejam produzidos até o final de 2023, registrando um crescimento de 2,6% em relação ao ano anterior.
Este cenário reforça a importância de adotar processos e matérias-primas inovadores para atender às exigências de um mercado e consumidores cada vez mais exigentes. Dessa forma, o poliuretano se mostra como um ótimo aliado para sua empresa se destacar no setor!
Fale ainda hoje com nosso time de especialistas e saiba como inovar no mercado calçadista com nossas tecnologias em poliuretano.